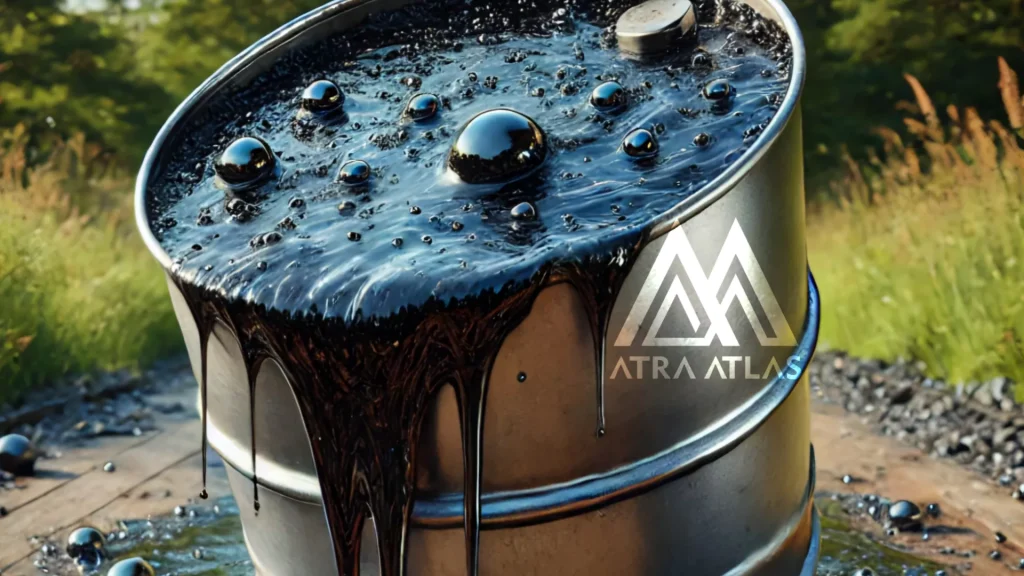
Types of Bitumen Grades
What is Bitumen? Bitumen: Properties and Uses
Bitumen is a black, sticky substance used for waterproofing and asphalt production. There are various grades of bitumen, and it’s used in construction materials, decorative items, artificial prosthetics, waterproofing ships, and even mummification. Bitumen is derived from petroleum.
Bitumen naturally occurs under the earth’s crust, appearing as springs, lakes, and surface mines in both solid and liquid forms. In ancient times, natural bitumen was used by our ancestors and became widely used in road construction by the late 19th century. With the discovery and refining of petroleum, resulting in bitumen residues, the path was paved for extensive bitumen use in road construction.
Asphalt surfaces made with bitumen today create smooth and safe roads for light and heavy vehicles, high-quality runways for aircraft landings and take-offs, and excellent rail foundations for trains.
Building waterproofing materials and industrial applications, such as protective coatings for oil and gas pipelines and power lines, highlight bitumen’s covering and waterproofing capabilities.
Ingredients of Bitumen
Composition and Properties of Bitumen
The various components of bitumen are not yet fully understood, but the main components that have been separated from bitumen using various solvents are asphaltenes, resins, and heavy oils, which are sometimes accompanied by a small amount of minerals and are situated in an oily colloidal environment next to each other.
The flexibility and adhesiveness of bitumen are attributed to the resins. On the other hand, the more asphaltenes there are, the harder the bitumen, but with an increase in oils, the bitumen becomes softer. By heating bitumen, the oily substances turn into resins, and the resins further transform into asphaltenes. At excessive heat, bitumen converts into coal and water vapor.
The various components of bitumen are not yet fully understood, but the main components that have been separated from bitumen using various solvents are asphaltenes, resins, and heavy oils, which are sometimes accompanied by a small amount of minerals and are situated in an oily colloidal environment next to each other.
The flexibility and adhesiveness of bitumen are attributed to the resins. On the other hand, the more asphaltenes there are, the harder the bitumen, but with an increase in oils, the bitumen becomes softer. By heating bitumen, the oily substances turn into resins, and the resins further transform into asphaltenes. At excessive heat, bitumen converts into coal and water vapor.
Asphaltene
Asphaltene is a brittle solid that is insoluble in normal heptane and ranges in color from black to brown. In addition to carbon and hydrogen, it contains small amounts of nitrogen, sulfur, and oxygen. Asphaltene is generally considered a very polar compound and consists of complex aromatic substances with very high molecular weight.
It does not have a specific melting point, and when heated, it first swells, then decomposes, and ultimately leaves a lot of carbonaceous residue.
Asphaltene makes up between 5 to 25 percent of bitumen. The higher the amount of asphaltene in bitumen, the harder and less penetrable the bitumen becomes, in addition to having a higher softening point and ultimately higher viscosity. The molecular weight of this substance ranges widely from 600 to 300,000, depending on the separation method applied.
- Maltans
Maltens are the soluble components in light solvents like normal heptane. In bitumen, maltens are a mixture of two parts: resins and oils. The molecular weight of the components of maltens ranges from 250 to 1,250 grams per mole.
- Resins
Resins are soluble in normal heptane. Most of these compounds, like asphaltenes, are composed of carbon and hydrogen and also contain small amounts of oxygen, sulfur, and nitrogen. This substance is a dark brown, solid, and semi-solid, and is very polar. The unique property of resins is that they are highly adhesive.
Resins are considered anti-coagulants for asphaltenes, and the ratio of resin to asphaltene can affect the bitumen, giving it a sol or gel-like state.
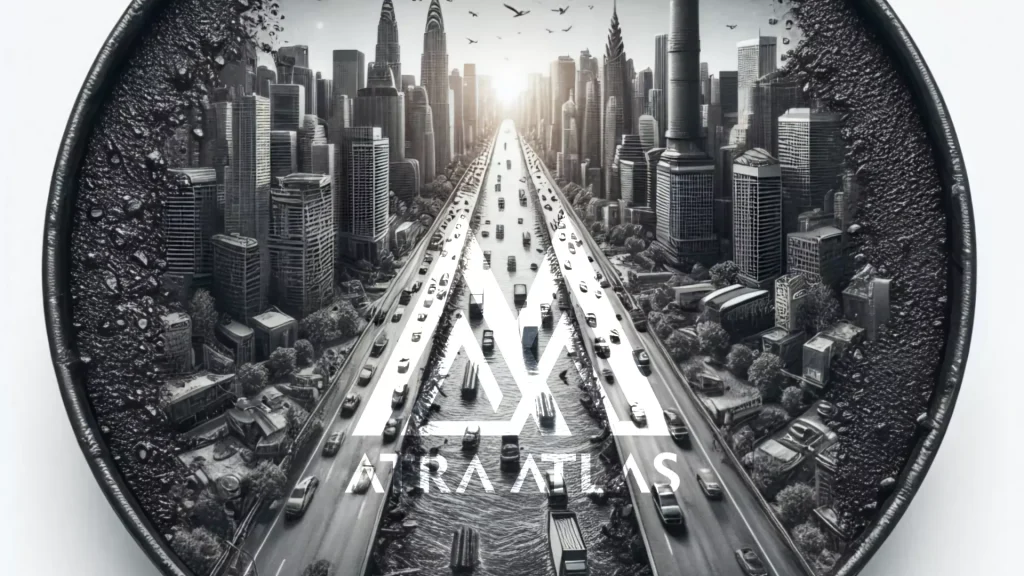
- Aromatics
Aromatics are cyclic compounds with the lowest molecular weight and include aromatic or naphthenic side chains. They are considered a very suitable anti-coagulant environment for asphaltenes. This component makes up between 40 to 60 percent of the total bitumen and is a viscous, dark brown liquid with a molecular weight ranging from 300 to 2,000.
Aromatics contain non-polar carbon chains in which saturated rings predominate, providing a high solubility capacity for other heavy hydrocarbons.
Saturated Compounds:
Saturates are composed of straight-chain and branched aliphatic hydrocarbons, along with alkyl naphthenes and some alkyl aromatics. These compounds are often viscous oils, non-polar, and colorless.
Their average molecular weight is similar to that of aromatics, and their components include both waxy and non-waxy saturates. This fraction makes up 5 to 20 percent of bitumen.
In general, asphaltenes form the structural backbone of bitumen, while resins contribute to its adhesiveness and malleability. Oils affect the fluidity of bitumen. Essentially, the physical properties of bitumen are determined by the chemical structure, quantity, and quality of its hydrocarbons.
Uses of Bitumen:
Bitumen is commonly used in two main areas: road construction and waterproofing. Approximately 90% of the produced bitumen is utilized in road construction, while waterproofing applications account for only 10% of bitumen consumption. These include:
Floor coating
Roofing
Underground pipelines
Metal protection
Sealing tanks, channels, bridges
Stabilizing loose sands
Painting
Petroleum Asphalts
These types of bitumen originate from crude oil. They are solid or semi-solid bitumen that are directly obtained from the distillation of crude oil or through additional processes such as air blowing. Compared to other types of bitumen, these have more applications and higher consumption.
Blown bitumens:
Petroleum-based bitumen is produced using two methods: Straight Run and Air Blowing. The Air Blowing method is used when the initial bitumen material (feedstock) does not meet the expected properties. In this case, by blowing air into the feedstock at temperatures between 190-200°C, a product with modified properties is produced.
This process is sometimes called Asphalt Oxidation, and the product is known as Oxidized Asphalt, but the terms Air Blowing and Air Blown Asphalt are more appropriate. In this process, polymerization and dehydrogenation occur, and except for very small amounts, oxygen does not enter the air-blown product.
In the industry, bitumen is produced using two methods: Continuous Process and Batch Process.
The produced bitumen is categorized and named based on its air blowing level according to tests that comply with global standards.
The most recognized global standards are Viscosity Grade, Penetration Grade, and Performance Grade.
The primary raw material for producing petroleum bitumen is the residue from the vacuum distillation tower (known as Vacuum Bottom or VB), which is used to produce various grades of bitumen such as 60/70, 85/100, and other bitumen grades.
1- Batch Process
In the Batch Process, the oxidizing tower is filled with a specific volume of feedstock. After blowing air under predetermined conditions (reaction temperature, time, and feedstock amount) and achieving the desired product specifications, the tower is emptied, and the product is transferred to the appropriate tanks.
The main components of the batch air blowing unit are:
1.Pre Heater
2.Blower or Compressor
3.Oxidizer Tower
4.System for Collecting and Burning Vapors
2- Continuous Process
In the Continuous Process, the feedstock enters the oxidizing tower continuously at a controlled flow rate and pre-determined temperature. After air blowing under constant operating conditions, the product is continuously discharged from the oxidizing tower. This method of producing bitumen, used in refineries, is favored for the following advantages:
Reduced pollutant vapors
Lower equipment and maintenance costs
Increased efficiency and production rate per unit time
Reduced thermal load on pre-heaters
Ease of control and process operations due to the continuous nature of the process
Less air consumption and shorter air blowing time due to the optimal use of blown air
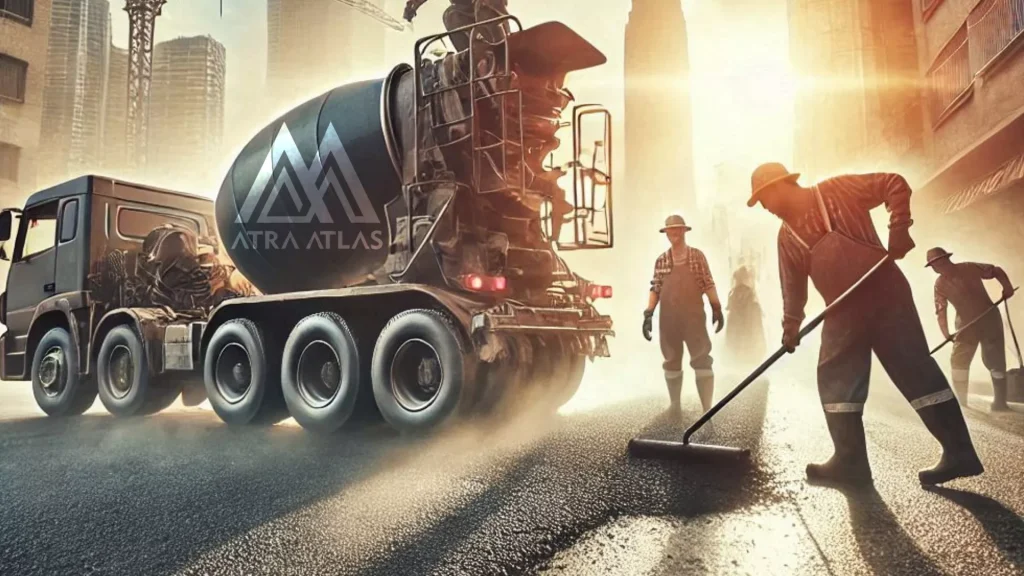
The key uses of bitumen are due to its two important properties:
1.Water impermeability
2.Adhesiveness
Bitumen is usually obtained from the distillation of crude oil. This type of bitumen is called petroleum bitumen or distillation bitumen. Petroleum bitumen is a product of two stages of crude oil distillation in the distillation tower.
In the first stage of distillation, light materials like gasoline and propane are separated from crude oil. This process occurs at a pressure close to one atmosphere.
In the second stage, heavy compounds like diesel and kerosene are removed. This process is carried out under a vacuum pressure. In the end, a mixture of very fine solid particles called asphaltenes remains, which are immersed in a greasy fluid called maltene.
However, some types of bitumen are naturally occurring, formed by the gradual transformation of crude oil and the evaporation of its volatile components over many years. This type of bitumen is called natural bitumen and has a longer lifespan compared to petroleum bitumen. Such bitumen may exist in pure form in nature (lake bitumen) like Lake Behbahan in Iran and Lake Trinidad in the USA, or be extracted from mines.
How is Bitumen Produced:
- 1.Direct Execution
- 2.Air Blowing, which can be done as either a batch or continuous process.
Types of Bitumen Grades, Sources, and Uses:
Bituminous materials are more diverse than crude oil alone, as bitumen has other sources besides oil. Depending on the origin, bitumen is divided into three categories:
- 1.Natural Bitumen
- 2.Petroleum Bitumen
- 3.Tar Bitumen
Until the end of the 19th century, the bitumen used in road and street construction was of various types such as mineral bitumen, bituminous rocks, mastic bitumen, and powdered stone, which are considered mineral or natural bitumen.
In the early 20th century, petroleum bitumen derived from refining crude oil entered the market and replaced mineral and natural bitumen in asphalt pavements and other industrial uses.
Direct extraction of bitumen from crude oil:
Distillation and Production Process of Bitumen
Distillation is a fundamental process in the refining of crude oil. The first stage of distillation is carried out under atmospheric pressure and typically involves heating crude oil to about 650 to 800 degrees Fahrenheit and then injecting it into a separation column.
This way, lighter fractions are collected as the overhead product of the column, and the bituminous residue is referred to as atmospheric residue. This is the first stage in the entire refining process. Many crude oils contain high percentages of high boiling point fractions that cannot be distilled in an atmospheric distillation unit. To separate these fractions and produce bitumen with the desired characteristics, a secondary separation column operating under vacuum conditions is used.
The residue from this process is known as straight-run bitumen. The production of asphalt using the vacuum distillation method has very little impact on the other properties of bitumen, except for permeability. The origin of the crude oil used also significantly affects the physical properties of the produced bitumen.
What is the Use of Vacuum Bottom Bitumen?
Vacuum Bottom Bitumen Uses:
Crude oil is refined in refineries to obtain petroleum derivatives. This oil is transferred to distillation towers in the refinery and separated into its constituent parts. The reason for the separation of crude oil components is the difference in boiling points at different levels of the tower.
The lowest layer remaining from the distillation of crude oil under vacuum conditions in distillation towers is called vacuum bottom (VB). In the past, this vacuum bottom was known as crude oil sludge and was discarded.
Over time and with technological advancements, engineers managed to convert vacuum bottom into a usable substance through specific processes. In fact, the material derived from vacuum bottom is bitumen and fuel oil. Vacuum bottom (VB) constitutes about 70% of the raw material for fuel oil.
Over time and with technological advancements, engineers managed to convert vacuum bottom into a usable substance through specific processes. In fact, the material derived from vacuum bottom is bitumen and fuel oil. Vacuum bottom (VB) constitutes about 70% of the raw material for fuel oil.
What are the Characteristics of Vacuum Bottom Bitumen?
Vacuum bottom has an appearance and smell similar to bitumen and is produced in a dark color. This substance is chemically stable but flammable. Vacuum bottom is composed of hydrocarbons that have more than 35 atoms.
The temperature of the vacuum bottom in distillation towers ranges between 240 to 320 degrees Celsius. When air passes through the vacuum bottom at this temperature, the oxidation process begins. The result of blowing air into the vacuum bottom is the improvement of its properties and the transformation of maltene molecules into heavier molecules, which are asphaltenes. This molecular transformation leads to the creation of bitumen with low penetration grade and increased smoothness.
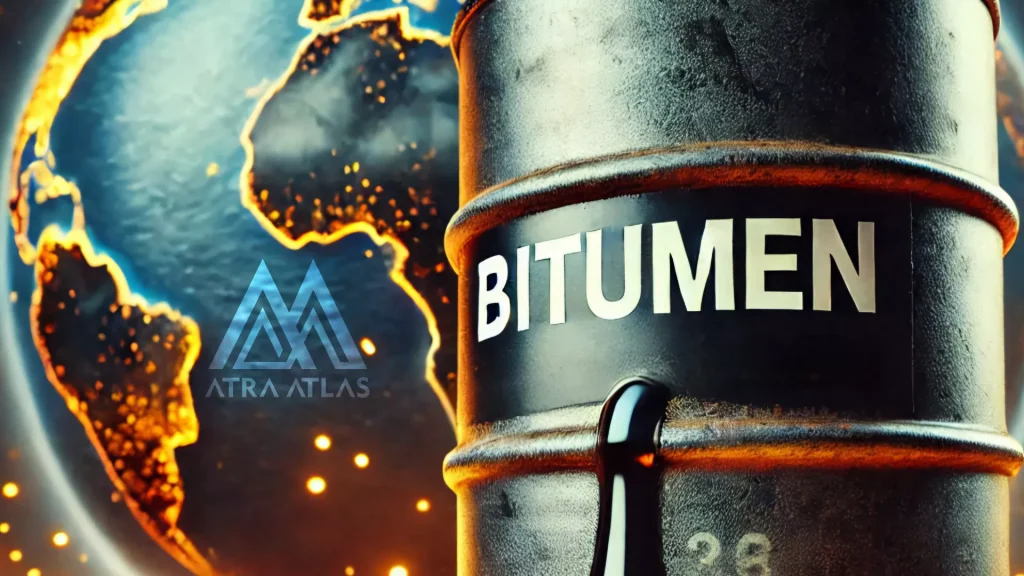
Characteristics of Vacuum Bottom
The other characteristics of vacuum bottom obtained in distillation towers include:
- 1.Density at ambient temperature (25°C): 1010-1020 kg/m³
- 2.Penetration grade: 22-33 mm
- 3.Viscosity at 100°C: 450-900 centistokes
Uses of Vacuum Bottom
Vacuum bottom is used in the production of fuel oil and bitumen, meaning it is the raw material for these two products.
Modified Bitumen
To achieve suitable mechanical properties, a polymer modifier is used to change the natural rheological properties of bitumen. The widespread use of plastics and rubbers in various sectors such as industry, agriculture, and even daily life has led to significant polymer waste and important environmental issues.
To address this problem, new methods have been explored. From an economic and environmental perspective, it is cost-effective to use waste polymers as bitumen modifiers, such that the properties of bitumen modified with waste polymers are similar to those modified with first-hand polymers.
There are two categories of waste polymers:
Thermoplastic waste polymers
Thermosetting waste polymers
Adding such polymers to bitumen leads to improved thermomechanical resistance. Polypropylene and EVA also increase the elasticity and adhesiveness of bitumen.
Regarding thermosetting waste polymers (such as rubber powder from waste tires), CTR is considered the best example of this type. Vestenamer polymer (poly-octenamer) is used as a polymer additive only in combination with rubber powder. This polymer facilitates the modification of asphalt with rubber powder.
Emulsion Bitumen)
Emulsion bitumen is obtained by mixing bitumen, water, and an emulsifier. The amount of emulsifier is very small, about 0.3 to 0.5 percent of the bitumen weight. The amount of water used in this type of bitumen is about 30 to 50 percent of the bitumen weight.
The emulsifier is usually an alkaline salt of organic acids or ammonium salt, which charges the bitumen particles. Thus, the bitumen particles repel each other due to the induced charge and float as spheres with a diameter of one-hundredth to one-thousandth of a millimeter in the water.
Advantages of Using Emulsion Bitumen:
Environmental Pollution Reduction: There is no need to use petroleum or flammable solvents.
Reduced Fire Hazard: During the transportation of bitumen.
Emulsion bitumen can be used instead of MC bitumen after the road subgrade has been completed and before the asphalt layer is spread. It is also used for the production of concrete asphalt or waterproofing. Another use of this product is in agricultural fields to prevent water evaporation and reduce soil moisture loss.
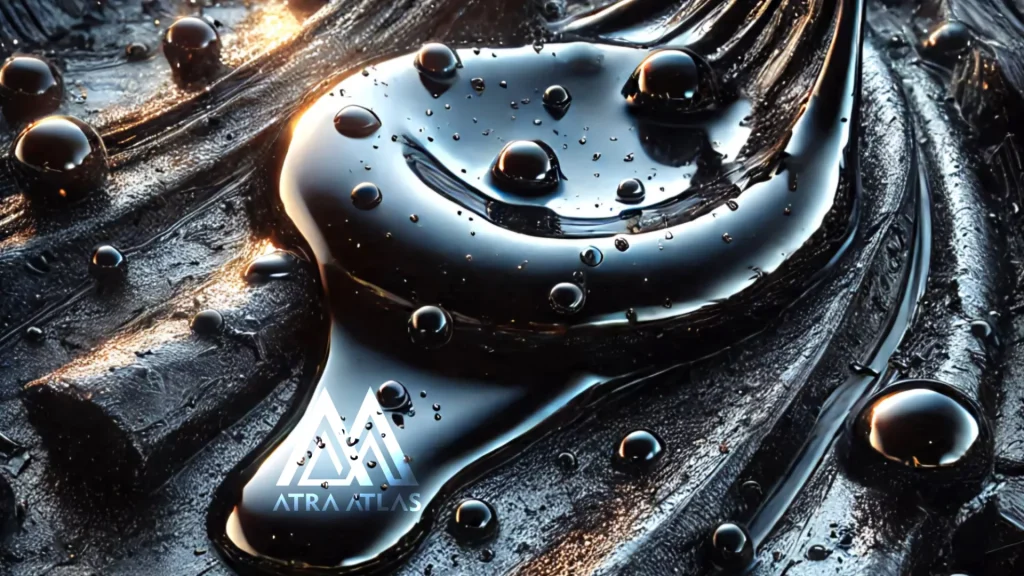
Soluble Bitumen:
Soluble bitumen is a mixture of bitumen and a suitable solvent (e.g., kerosene or gasoline). The type and quality of soluble bitumen depend on the quality of the original pure bitumen, the type of solvent, and the amount of solvent. This bitumen is either liquid at ambient temperature or becomes liquid with a little heat.
Applications of Soluble Bitumen
Soluble bitumen is used in various coating asphalts. The setting or hardening speed of this type of bitumen depends on the type of solvent. The lack of heating equipment, decomposition at high temperatures, cooling during work, inability to penetrate porous minerals, worker safety, and fire hazards lead to the use of soluble bitumen in some cases.
Uses of Soluble Bitumen
Soluble bitumen is used in road construction for surface coatings, penetration, cold asphalt from factories, or on-site mixtures.
Types of Soluble Bitumen Based on Setting Speed and Solvent Type:
- 1.Rapid Curing (RC) Bitumen
- Due to the high evaporation rate of gasoline, the bitumen dissolved in gasoline hardens faster. This bitumen is termed rapid curing bitumen.
- 2.Medium Curing (MC) Bitumen
- Bitumens dissolved in kerosene are termed medium curing bitumens, as kerosene evaporates slower and over a longer period compared to gasoline.
- 3.Slow Curing (SC) Bitumen
- Bitumens dissolved in diesel or fuel oil are termed slow curing bitumens.
Production Processes of Petroleum Bitumen:
Petroleum bitumen is produced using three processes:
- 1.Straight Run
- 2.Air Blowing
- 3.Blending
Specifications of Bitumen Grades
Properties of Bitumen
1.Penetration Grade: The penetration test is used to determine the hardness of bitumen. In this test, a standard needle under a load of 100 grams penetrates the bitumen at a temperature of 25 degrees Celsius for 5 seconds. The lower the penetration, the harder the bitumen.
2.Viscosity: The higher the viscosity of bitumen, the more solid properties it exhibits. At higher temperatures, the viscosity decreases. This property of bitumen is measured using the Saybolt Furol device or by the kinematic method.
3.Flash Point: The flash point is the temperature at which, if bitumen reaches that temperature, the gases emitted from it ignite when exposed to a flame. The maximum temperature to which bitumen can be heated in the workshop is limited by the flash point.
4.Weight Loss: The weight loss of bitumen at high temperatures is due to the evaporation of some of its oils and petroleum compounds. The weight loss of bitumen is measured in an oven at 163 degrees Celsius for 5 hours.
5.Ductility: If a sample of bitumen with a cross-sectional area of 1 square centimeter is pulled at a speed of 5 centimeters per minute, the amount of elongation before breaking is called the ductility of the bitumen.
6.Purity: The solvents for bitumen are carbon tetrachloride and sulfur carbon. If a sample of bitumen is dissolved in these materials, its impurities remain, and from this, the purity of the bitumen is determined.
7.Softening Point: The softening point is the temperature at which bitumen transitions from a solid to a fluid state. The higher the softening point, the less sensitive bitumen is to temperature changes. The softening point of ordinary bitumen is around 60 to 70 degrees Celsius.
Applications of Bitumen in Road Construction
Bitumen’s adhesiveness and waterproofing properties have led to its widespread use in all aspects of civil engineering and construction. Penetration bitumen and emulsion bitumen are used for constructing railway tracks, while polymer-modified bitumen is used in the railway industry to reduce noise and vibration.
Three Other Applications of Bitumen:
1.Airport Runways: Due to the strong structure of PMB, which is polymer-modified bitumen.
2.Marine Construction Industry: Includes coating channels, underground tunnels, riverbank protection, and constructing dams and piers in the sea.
3.Other Applications: Includes roofing felt materials, printing ink, packaging paper, electrical cable insulation, junction boxes, and more.
Import Sales of Bitumen
Iran is the largest producer of bitumen in the Middle East. Our country annually imports over 4 million tons of bitumen in various packaging and transportation methods. The number of target import destinations for bitumen reaches more than 30 countries. The production capacity of bitumen in our country exceeds 6 million tons, of which about 2 million tons are consumed domestically.
For importing various grades of bitumen, you can utilize the consultation and experience of Atara Atlas Trading Company.
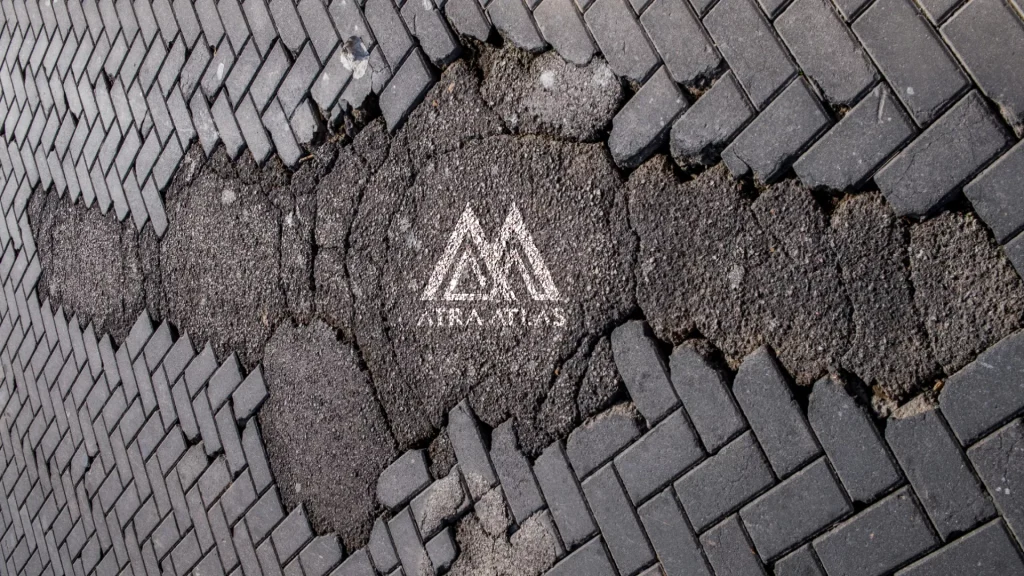
How is Bitumen imported from Iran?
Bitumen import from Iran are conducted through sea and land routes using bulk, barrel, and bag packaging. Bulk bitumen is import by tankers via land routes and by ships via sea routes.
Barrels: Available in sizes of 150 kg, 185 kg, and 22 kg.
Jumbo Bags: Jumbo bags are an environmentally friendly and cost-effective type of packaging available in various sizes.
Bitumen Grades and Their Applications in Brazil
VG30 Bitumen: This type of bitumen is obtained from air blowing vacuum bottom from the distillation tower and is classified based on viscosity. The primary use of this type of bitumen is in road construction, waterproofing, building construction, and the production of liquid bitumen. VG30 bitumen is more suitable for regions with moderate climates.
Classification Based on Viscosity
In viscosity-based classification, bitumens are ranked based on absolute viscosity at 60°C and kinematic viscosity at 135°C. Absolute viscosity is expressed in poises and kinematic viscosity in centistokes. The classification and specifications of pure bitumen are reported in AASHTO-M226 and ASTM-D3381 standards.
Bitumen Production Process
Distillation is an essential process in refining crude oil. The first stage of distillation is performed under atmospheric pressure and involves heating crude oil to about 650 to 800 degrees Fahrenheit and then injecting it into a separation column.
This way, lighter fractions are collected as the overhead product of the column, and the bituminous residue is referred to as atmospheric residue. This is the first stage in the entire refining process. Many crude oils contain high percentages of high boiling point fractions that cannot be distilled in an atmospheric distillation unit. To separate these fractions and produce bitumen with the desired characteristics, a secondary separation column operating under vacuum conditions is used. The residue from this process is known as straight-run bitumen.
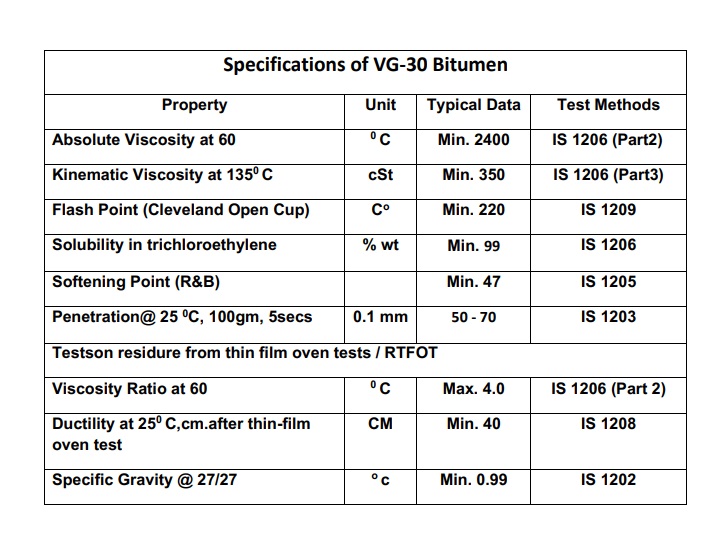
VG40 Bitumen
VG40 Bitumen is one of the types of bitumen classified based on viscosity. Viscosity is a fundamental property of bitumen that determines how the material behaves at a specific temperature or within a temperature range. In terms of usage, VG40 bitumen is more suitable for regions with warmer climates.
Classification Based on Viscosity
In viscosity-based classification, bitumens are ranked according to the absolute viscosity at 60°C and kinematic viscosity at 135°C, with specific technical criteria established for each.
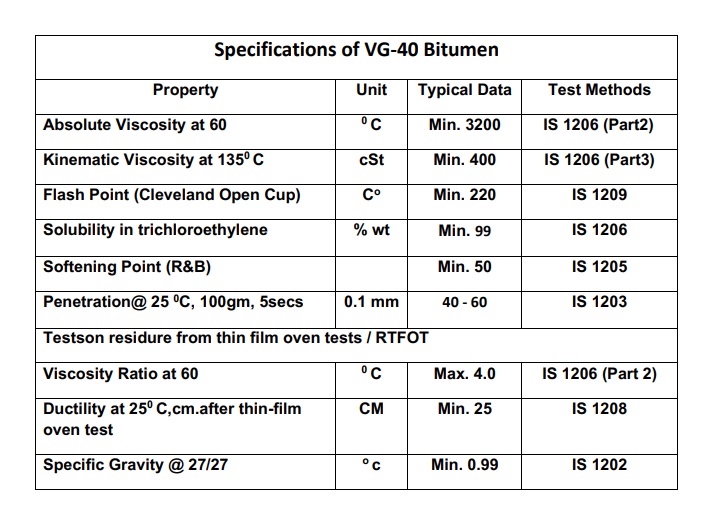
50-70 Bitumen Grade
50-70 bitumen is obtained through the oxidation process on vacuum bottom (the raw material for bitumen production obtained from the residue of the vacuum distillation tower in oil refineries) in bitumen production units.
The penetration grade of this type of bitumen (a test to determine the hardness of bitumen) is between 50 to 70.
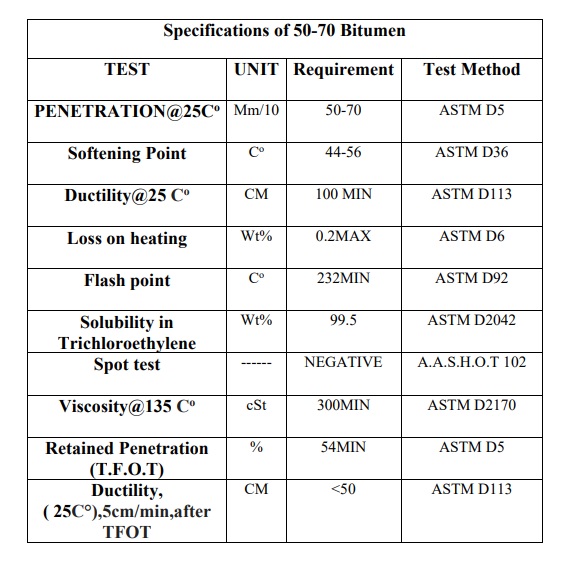
60-70 Bitumen Grade
60/70 Bitumen is a type of penetration bitumen produced by using the oxidation of vacuum bottom. Penetration bitumen or road grade bitumen is used for the production of asphalt.
Penetration bitumens are obtained by performing the air-blowing process on the residue of the distillation tower, known as vacuum bottom. Since the penetration grade of this type of bitumen is between 60 to 70, it is known as 60/70 bitumen. 60/70 bitumen is more suitable for moderate climates.
The state of 60/70 bitumen depends on its temperature. The temperature and hardness of bitumen depend on the type of crude oil and its refining method. The penetration grade of 60/70 bitumen is between 6 to 7 millimeters, making it a heavy bitumen suitable for road construction and repair.
60/70 bitumen is used for the production of asphalt and is primarily used in the production of hot asphalt for surface coating. 60/70 bitumen is the most widely used among the various types of bitumen and is a raw material for other bituminous products.
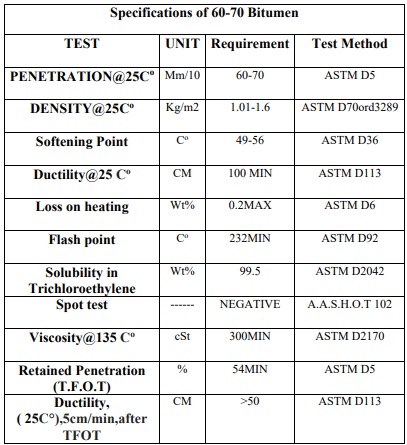
80-100 Bitumen Grade)
80-100 Bitumen is fully soluble in carbon disulfide (CS2) and possesses adhesiveness and waterproofing properties. This material is primarily composed of hydrocarbons, usually containing 80% carbon and 15% hydrogen, with the balance comprising oxygen, nitrogen, and other trace elements.
Penetration grade bitumen is typically used on road surfaces and in minor industrial applications. The penetration hardness of bitumen is determined by measuring the depth to which a standard needle penetrates vertically in 5 seconds. This test is conducted on a sample of bitumen maintained at a temperature of 25 degrees Celsius.
(Applications of 80-100 Bitumen Grade)
Viscosity grade asphalt: It can be used on the main asphalt with AC grades (asphalt cement) or old residual grades AR (aged residual).
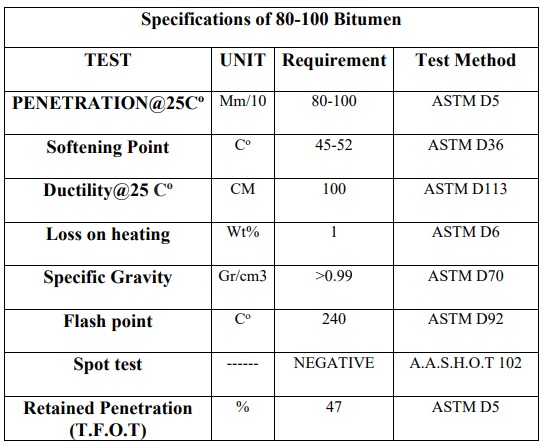